Bearing Failure Analysis
Indicators of Bigger Issues
Bearings are among the most critical components for the safe and reliable operation of rotating machinery. While fluid film bearings are designed for infinite life under design conditions, they are also designed to be a sacrificial component in case of upset conditions. Therefore, any issues with the machine will likely manifest at the bearings.
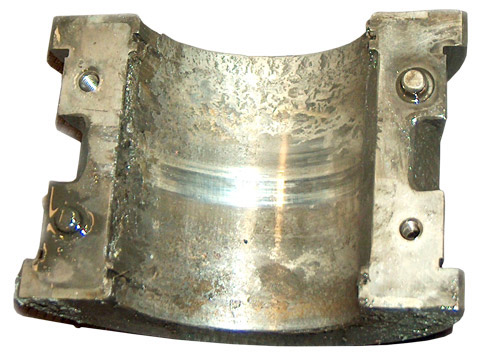
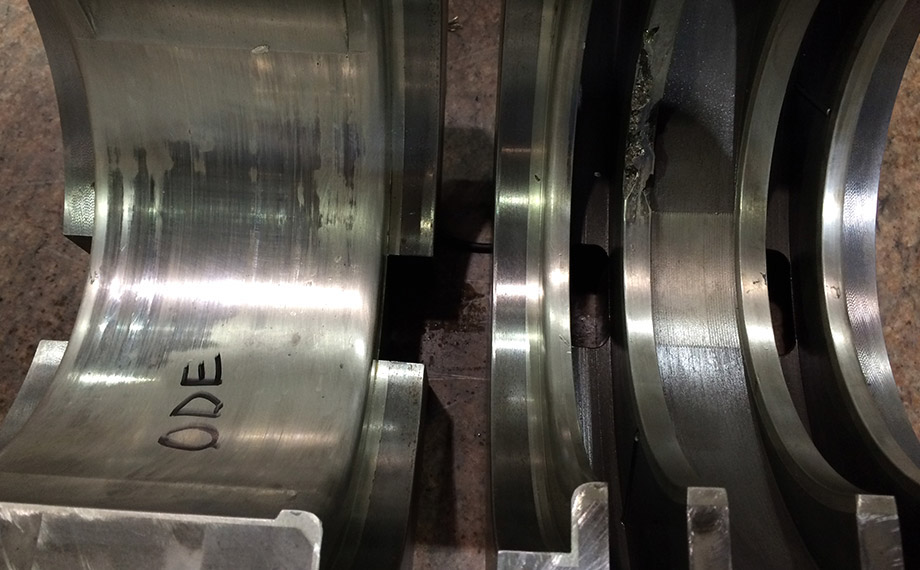
Finding the Cause
Bearing failure analysis helps pinpoint the cause and mode of failure in order to eliminate or otherwise address it, and thus maximize machine uptime. The analysis process will typically include:
- Visual examination of the failed component, as well as any specific conditions found upon disassembly
- Laboratory analysis of oil samples and/or any embedded particles
- Evaluation of operating data, such as vibration levels, oil outlet and bearing temperatures, and pressures
- Review of any relevant incident that may have preceded the failure
- Review of any history of failures, recent modifications or change in operating conditions
- Sequence of events leading to the failure
Frequently, more than one factor combines to result in a failure, and a complete picture of the operating conditions and background can help identify the issue(s).
Common Types of Failure Analyzed
- Babbitt fatigue
- Bond failure
- Brinelling and fretting wear in bearing pads and shells
- Babbitt wiping and overload conditions
- Babbitt creep and thermal ratcheting
- Cavitation damage
- Electrical shaft current damage
- Scoring by foreign matter or dirt
- Corrosion damage
- Pad flutter
- Porosity and blisters in babbitted bearings
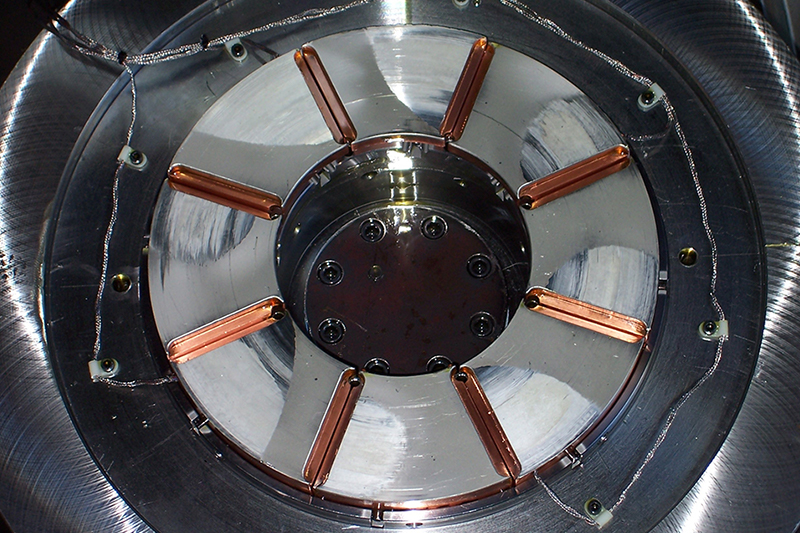
Bearing Repairs
Bearings Plus provides complete replacements, repair and rebabbitting for tilt pad and fixed profile bearings, all backed by robust quality inspections.