Bearing Damage Index
Scoring
Contamination of the lubricant – or ‘dirt’ – may cause polishing of the surfaces of babbitt-lined bearings, burnishing of bronze bearings, abrasive wear of overlays or other bearing linings, and scoring of both bearing and mating surfaces. The degree of severity depends on the nature and size of the dirt particle, as well as oil film thickness and type of bearing material.
Contamination of the lubricant can result from:
- Built-in dirt on housings, shafts, oil galleries, etc., present at the time of machine assembly
- Entrained dirt entering through breathers or air filters
- Particles derived from the combustion of fuel in internal-combustion engines where the lubrication system is shared with the driven machine
- Metallic wear particles resulting from abrasive wear of moving parts
Addressing the Damage
Depending on the bearing condition, bearings may need to be scrapped or relined and the replacements fitted after cleaning the journal, oil ways and filters; or the bearings may be able to be re-fitted after they and the journal surfaces have been cleaned, provided clearance increase due to wear can be tolerated. In either case, consideration should be given to improving the level of full-flow filtration or installing a by-pass centrifugal filter.
Unless the design life of the equipment or acceptable service intervals are consistent with the expected rate of wear in the bearings, not many bearing solutions can perform satisfactorily in a contaminated environment.
For new machine designs where filtration is not a viable solution, there are a couple of options to prolong bearing life in a contaminated bearing environment:
- Active magnetic bearings, where the components can be protected by a stainless steel ‘can’ between them and the contaminated gas or liquid
- Ceramic fluid film bearings, where the mating surfaces are normally monolithic silicon carbide, which is resistant to abrasion by contaminants in the lubricant (such as sand particles)
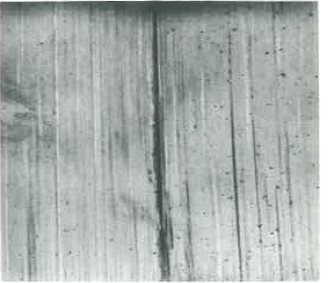
Figure 1: Whitemetal-lined bearing scored and pitted by ‘dirt’
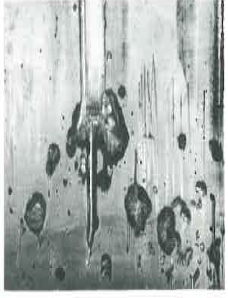
Figure 2: Whitemetal-lined bearing showing ‘haloes’ caused by ‘dirt’ particles
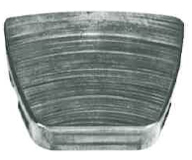
Figure 3: Concentric scoring of thrust pad due to ‘dirt’ entering bearing at high speed
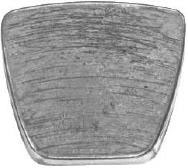
Figure 4: Scoring due to ‘dirt’ entering bearing set up
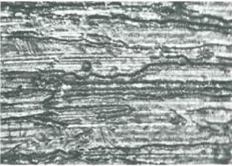
Figure 5: Surface of figure 4 pad at higher magnification showing irregular tracks caused by rolling of shot blast spherical steel particles