Bearing Upgrades
Addressing Your Challenges Through Upgrades
Bearings Plus provides replacements and upgrades for both fixed profile and tilt pad bearings, and offers proprietary product solutions to improve stability, control vibrations, eliminate pivot wear and address a myriad of other challenges.
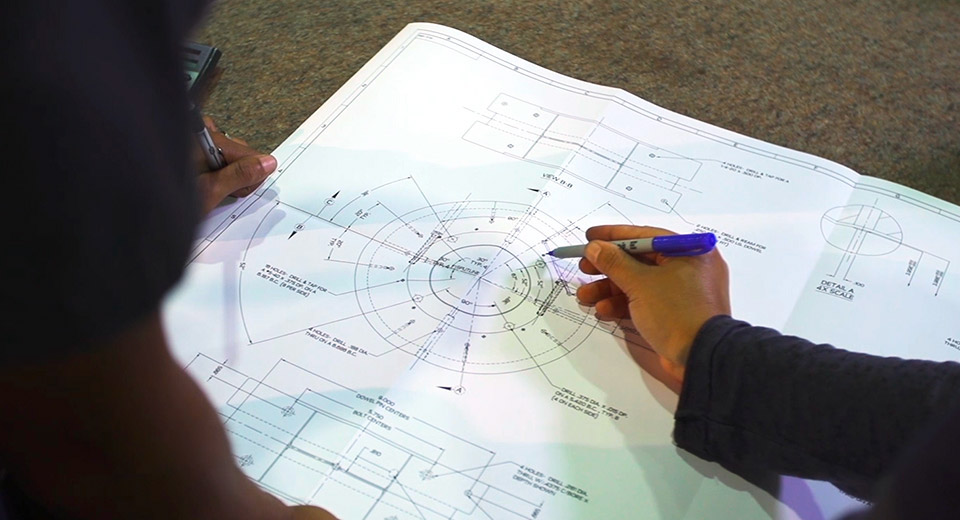
BPI has upgraded bearings on numerous integrally geared compressors, multi-stage compressors, blowers, fans, steam and gas turbines, expanders, motors, generators, pumps and gearboxes. Our past successes speak for themselves. Below are a few examples.
- Resolved high bearing temperature and bearing wiping of 60 mm (2.3622″) 5-pad load on pad (LOP) tilt pad journal bearing for an integrally geared compressor at 24900 rpm by upgrading to a 4-pad load between pad (LBP) tri-metal Flexure Pivot bearing.
- Upgraded 101.6 mm (4″) pressure dam journal bearing of a rerated compressor at 8139 rpm to a ball and socket bearing with optimized bearing clearance to accommodate rerated compressor capacity.
- Upgraded 228.6 mm (9″) thrust bearing of a compressor at 7250 rpm to a polymer-lined thrust bearing to increase load capacity and temperature limit.
- For a compressor at 4734 rpm experiencing thrust bearing failure due to steam path fouling and high bearing temperature (110°C [230°F] at 4405 rpm and 23570 lb thrust load), upgraded the 304.8 mm (12″) thrust bearing to a bearing with optimized pad geometry, keeping the temperature below 82°C (180°F) at 150% thrust load and full speed.
- Provided rotordynamic analysis of a blower experiencing high vibration due to operation close to critical speed. Upgraded the existing slinger ring lubricated journal sleeve bearings to tilt pad bearings to improve vibration behavior.
- Through lateral rotordynamic analysis, upgraded 76.2 mm (3″) pressure dam journal bearing of a steam turbine at 10000 rpm, which had subsynchronous vibration dependent on load condition and inlet oil temperature, to a Flexure Pivot radial bearing to eliminate subsynchronous vibrations.
- Upgraded 406.4 mm (16″) 4-pad LBP tilt pad journal bearing in a gas turbine at 3600 rpm, which had high bearing temperature due to inadequate oil path design. Provided optimum bearing clearance with upgraded pivot feature and oil flow to decrease bearing temperature and increase bearing life.
- Upgraded 295.275 mm (11.625″) taper-land thrust bearing to a low-profile self-equalizing tilt pad thrust bearing with optimum radial pivot location to maximize thrust load capacity within envelope size.
- Upgraded number one spherical fit journal bearing of steam turbine-generator train to an optimized tilt pad bearing through rotordynamic analysis for better stability and unbalance response and elimination of deterioration of spherical fit with time.
- Upgraded roller bearings to polymer tilt pad thrust bearings with 1 GPM oil flow for a pump at 3360 rpm.
- Upgraded 101.6 mm (4″) tilt pad journal bearing of HS gearbox pinion at 10000 rpm to tri-metal ball and socket tilt pad bearing for better stability, unbalance response and bearing temperature.
- Upgraded 120 mm (4.724″) 5-pad LBP tilt pad journal bearing of HS pinion rotor at 13000 rpm to CrCu backed offset pivot tilt pad bearing to reduce bearing temperature.
- Upgraded 177.8 mm (7″) journal sleeve bearing of HS gearbox pinion at 6620 rpm, which had high bearing temperature and high vibration at 12 to 13 MW, to optimized sleeve bearing to take 3.7 MPa unit load. Vibration behaviors were checked with detailed bearing analysis and rotordynamic analysis.
Related Products & Services
Flexure Pivot Journal Bearings
Flexure Pivot tilt pad journal bearings achieve high stability while eliminating pivot wear, high contact stresses and pad flutter that can affect conventional tilt pad designs.
Integral Squeeze Film Damper
Our patented ISFD technology provides precise stiffness and damping to meet rotordynamic requirements, and is suitable for both new and retrofit installations.
Ball and Socket Thrust Bearings
The full surface contact of the ball and socket pivot reduces stresses while providing the necessary stiffness and misalignment capability. This self-equalizing design ensures even loading across the thrust assembly.
Rotordynamic Analysis
Our full rotordynamic analysis evaluates bearing and seal characteristics simultaneously to better understand the independent effect of each component.
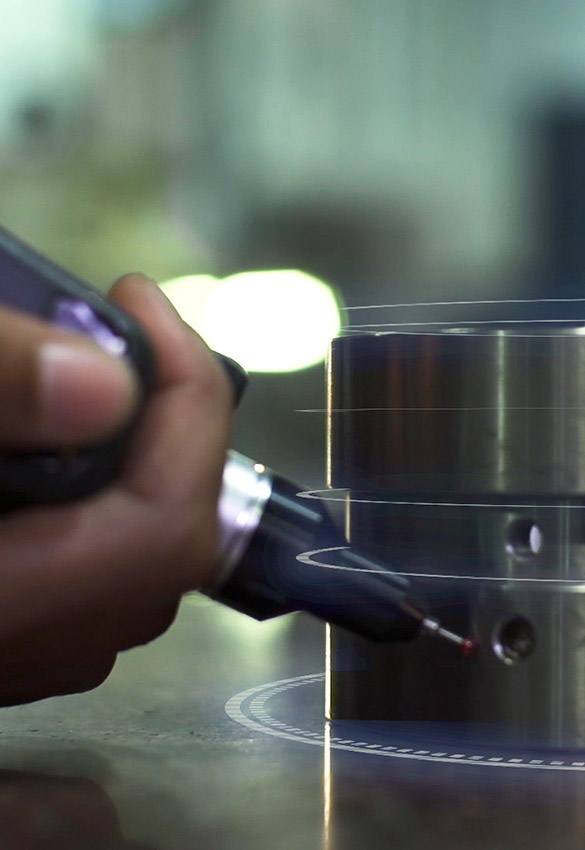