Bearing Damage Index
Fatigue
Fatigue results from having dynamic loads that exceed the fatigue strength of the bearing material at operating temperature.
Fatigue strength, especially of low-melting-point materials such as babbitt and lead-based overlays, is greatly reduced at high temperatures; hence, overheating alone may cause fatigue damage.
Other causes include overloading, cyclic out-of-balance loading due to overspeeding, and shafts that are not truly cylindrical due to manufacturing defects.
In whitemetal linings, fatigue cracks typically join to form pits with a characteristic rounded ‘molten’ appearance.
Addressing the Damage
As a first approach, investigate and rectify the causes of high temperatures or dynamic loading.
If the cause of dynamic loading cannot be eliminated, consider using a higher strength bearing material or implementing design changes to increase load capacity.
Bearing materials have been developed with various degrees of compromise between strength and conformability. Specifically, AS40 (40% tin/aluminum) and polymer linings provide much higher fatigue strength compared with babbitt, combined with good surface properties.
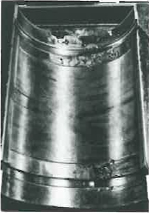
Figure 1: Whitemetal-lined, chambered top half turbine bearing with fatigue cracking on lands due to out-of-balance loading and excessively wide cut away
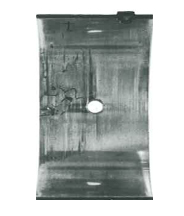
Figure 2: Fatigue cracking of whitemetal-lined bearing due to shaft deflection and edge loading
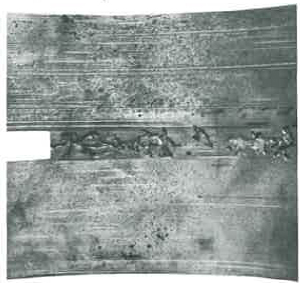
Figure 3: Fatigue cracking of whitemetal-lined bearing due to shaft ridging caused by differential wear in way of 180° groove